.aft structure .aft end structure .aftend structure .aft end construction .aft construction .aec
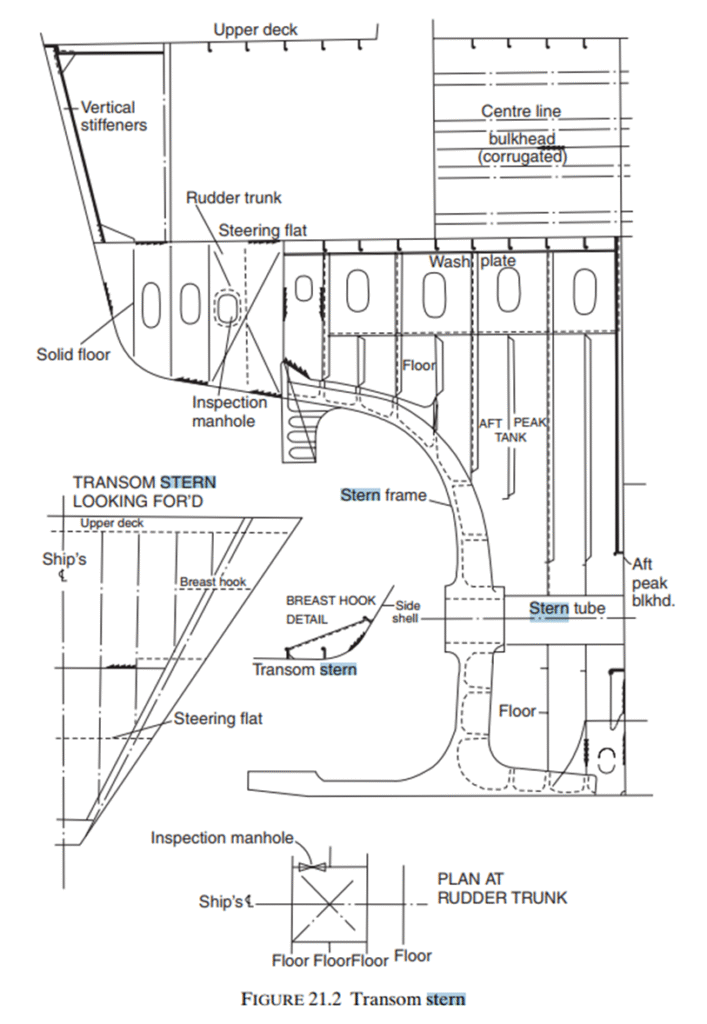
Considerable attention is paid to the overall design of the stern in order to improve flow into and away from the propeller. There are two types of stern. Cruiser stern, Transom stern. Cruiser stern used previously, but today most of these vessels have a transom stern. A cruiser stern presents a more pleasant profile and is hydrodynamically efficient, but the transom stern offers a greater deck area aft, is a simpler construction, and can also provide improved flow around the stern. Many forms of rudder are available, depending on the manoeuvering needs. Both the shape of the stern and the rudder type will determine the form of the stern frame, and this will be further influenced by the required propeller size. The propeller shaft and the rudder stock pierce the intact watertight hull, so particular attention should be given. The safety of the ship may depend on these arrangements.
Stern Construction:
.Stern Construction
Flat stern plating stiffened with vertical stiffeners. Deep floors and a centre line girder are provided at the lower region of the transom stern construction. Panting arrangements at the aft end are provided.
Stern Frame
.stern frame construction .sfc
The form of the stern frame is influenced by the stern profile and rudder type. To prevent serious vibration at the after end there must be adequate clearances between the propeller and stern frame, and this determines its overall size.
The stern frame of a ship may be cast, forged, or fabricated from steel plate and sections. On larger ships it is generally either cast or fabricated,
the casting done by a specialist works outside the shipyard. Larger stern frames cant be casted easily due to its bigger size. Also the transportation is a problem .So it may be cast in more than one piece and then welded together after bringing the pieces to the shipyard. Fabricated stern frames are produced by the shipyard itself, plates and bars being welded together to produce the stern frame.
Forged stern frames are also produced by a specialist manufacturer. And may also be made in more than one piece where the size is excessively large or shape is complicated. Sternpost sections are made streamlined form, in order to prevent eddies being formed behind the posts. Eddies can lead to an increase in the hull resistance.
Welded joints in cast steel sections will need careful preparation and preheating. Both the cast and fabricated sections are supported by horizontal webs. The connection of the stern frame to the hull structure is very important, the rotating propeller supported by the stern frame may set up serious vibrations. The rudder post is carried up into the main hull and connected to the transom floor which has an increased plate thickness. Also the propeller post may be extended into the hull and connected to a deep floor, the lower sole piece is carried forward and connected to the keel plate. Side shell plates are directly welded to the stern frame.