.rudder drop
Article link: https://sailorstaan.com/life-at-sea/jumping-clearance-and-its-purpose/
Rudder drop is defined as the wear down of the rudder carrier bearing as a result of the mechanical forces acting on it, namely buoyancy force (with which the rudder stock would ascend and damage the steering gear components), friction etc. The rudder drop would nullify the purpose of using the rudder carrier bearing which are supposed to reduce the friction during the rotation of the rudder stock during navigation. The rudder drop is measured using the trammel gauge.
How Rudder Drop measured ?
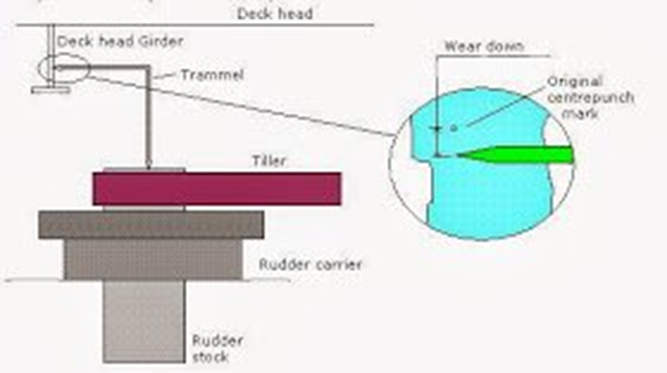
As We know that the drop is measured by a trammel gauge. The Trammel gage is an L-shaped instrument. Generally, a point marked on the rudder stock and another point is marked on the hull within the steering gear room (Here it is on the Deck head girder). The distance between these points shall be measured and recorded at the time of construction. The difference between the original and the measured points shall be referred to as the rudder drop or the rudder wear down as shown in the fig.
Measures to reduce the rudder drop
- More frequent greasing of the bearing
- Proving jumping clearance
- Regular care & maintenance of bearing
Jumping Clearance
Jumping Clearance is defined as the clearance or the distance between the pads one is welded onto the tip of the rudder and another one is on the hull opposite to the rudder pad. The jumping bar or the stopping bar is nothing but a rigid slab of metal which is being welded to the ship’s hull. Since, the bar needs to withstand heavy buoyancy force, acting on the rudder, it has to be made of high strength materials which has to be corrosion resistant and should be having a ductile nature.
Jumping clearance is increased due to rudder carrier bearing wear or rudder drop.
Why jumping clearance is provided:
- The maximum jumping clearance should always be less than the clearance between steering gear (the sliding ram) and the tiller arm.
- If the jumping clearance was not provided and no stopper, then it is very probable that the rudder would hit the hull with unimaginable force resulting to the damage of hull.
- Further, if the clearance is more because of the ascend, the rudder stock would hit the lower tiller which in turn strikes the sliding ram causing the ram to bend. In a nutshell, the entire steering system would break down. To prevent such undesirable situations to take place, jumping clearance is provided.
Rudder survey:
.rudder survey
Planning:
- Discussed with master and all officers.
- Discussed with office superintend
- Consult with dry-dock manager, safety officer, Repair manager
- Informed class surveyor regarding rudder survey.
- Risk assessment to be carried out.
- Work permit to be carried out.
- Check last dry-dock rudder service report.
- Tool box meeting carried out among engine staff.
- Wear proper PPE
- Arrange proper tools for taking all clearance.
Checks on rudder in dry-dock
- Rudder survey will be done only in dry-dock; it should be done only by shipyard workshop team with presence of surveyor.
- When ship enters dry dock and pumping out water, check water is coming out from rudder or not. If yes, then rudder is breached. If water ingress inside rudder, only the buoyancy of the rudder lost, no major casualty will occur. Internal parts of rudder might corrode.
- Carry out a visual inspection for crack on rudder plate.
- Open the top air plug and bottom drain plug in front of class surveyor. when water drain out it indicates crack in the rudder.
- So crack is detected by air pressure and applying soap solution.
- If the rudder is badly rusted or ship is older, surveyor may insist on thickness gauging of the rudder plate.
- Check the condition of the sacrificial anode on the rudder. And any masking tape or paint is over there.
- Check the cement on the palm coupling bolts for rudder and rudder stock. Remove the cement and check the condition of the palm nut.
- Check the rudder pintle clearance.
- Check the rudder jumping clearance.
- Check the rudder drop using trammel gauge.
- Check the rudder stock for corrosion and erosion
- Check condition of external rudder stop.
- Check the actual position of the rudder, compared to rudder angle indicator and see whether any difference is there by bending or deformations
- Now lower portion of the rudder is cut open and pintle nut is checked for proper securing and later the plates are welded and tested.
- Check the pintle bearing steel disc condition and drain passage clear or not.
- Hydraulic Pressures test the rudder at a water head of 2.45 meters.
- After draining and oiling the internal, plug the drain and check the effectiveness by a vacuum check and cement plug.
- Checked the rudder stock gland packing and renewed.
- For a new built ship, the standard clearance between pintle and bush is 1.5 mm.
For the ship in service, Maximum allowable clearances between pintle and bush is 6 mm. IF the actual clearance exceeds above 6mm, the bush should be renewed.
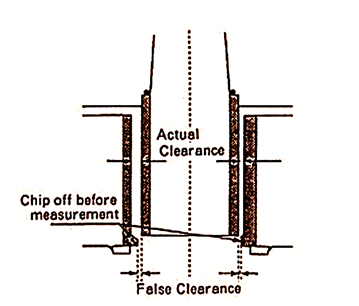
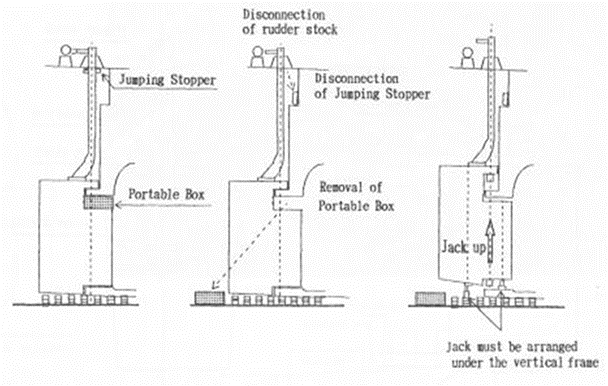
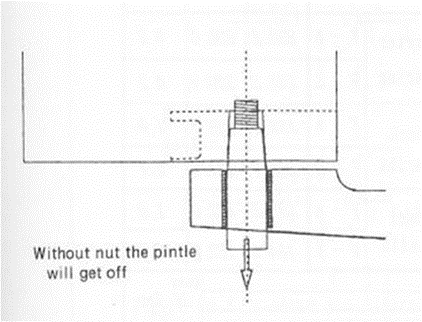
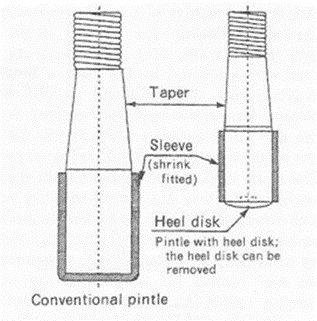
TESTS AFTER RUDDER REPAIRS
1. At the completion of the repairs, the rudder system is reassembled and function tests are carried out to ensure satisfactory operation before undocking.
2. If any work was done on the rudder body, it should be tested by compressed air to an equivalent pressure head of 2.45 m above the top of the rudder.
3. Other tests include swing the rudder from one extreme position to the other