.steel production method
.steel prod method
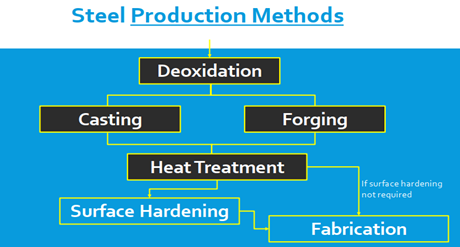
De-oxidation | Process | |
Killed | Steel has been completely deoxidized (oxygen removed) during liquid stage, by adding agent (aluminium) before casting, so that there is practically no evolution of gas during solidification. | |
Semi-killed | Steel is mostly deoxidized steel, however carbon monoxide leaves blowhole (porosity) distributed throughout the ingot. It is commonly used for structural steel with a carbon content between 0.15 – 0.25%. Structural steel is formed by “rolling” process, the process closes the porosity. | |
Rimmed | Steel has little or no deoxidizing agent added. |
Casting | Heating Iron Ore to liquid stage, add-in required agent, then pour the molten metal into mold to form shapes. |
Forging | Heating the steel into Austenite stage (plastic forms), then use mold to forcefully pressing / hammering (with high force) the metal into shape. |
Rolling | Heating steel plate / ingot(steel block) into Austenite stage (plastic forms), then use roller to forcefully pressing the steel plate / ingot into shape. |
Heat Treatment Process
.heat treatment process .htp
Heat Treatment | Process |
Annealing | Heat steel to recrystallize stage (>900oC), then cool it in furnace at very slow rate, to improve it’s ductility and higher elongation rate. |
Normalizing | Heat steel to recrystallize stage (>900oC), then cooled it in atmosphere, to make it less ductile, however improve tensile strength & toughness |
Quenching | Heat steel to recrystallize stage (>900oC),then cooled it rapidly using liquid (oil or water), as the carbon molecule unable to escape in time, it change into Martensite stage. Martensite steel is very hard, however brittle. |
Tempering | After quenching the steel, it is re-heated to below recrystallize stage (700 – 800oC), then cooled it in atmosphere, to make it regaining part of its’ ductility and tensile strength. |
Hardening of steel:
.hardening of steel
.steel hardening .wh
Work hardening is strengthening of metal by plastic deformation.
→ Case Hardening
Case Hardening Method | Process Description |
Flame Hardening | Heat the steel very rapidly with flame (>900oC), then quench (cooled rapidly) in water.It create a Martensite case on steel surface. Suitable for steel of carbon content 0.3-0.6%. The process cause steel to deform, and required tempering to restore steel core toughness. |
Carburizing | Heat the steel very rapidly with flame (>900oC) , then quench (cooled rapidly) in oil. It create a High Carbon Steel case on steel surface. Suitable for steel of carbon content 0.1-0.3%. The process cause steel to deform, and required tempering to restore steel core toughness. |
Nitriding | Heat the steel to approx. 500 – 600oC, then keep it in ammonia gas filled enclosed case. Nitride case will form on steel surface. The process cause very little steel deformation. Do not required further heat treatment for core material. |
Cyaniding | Heat the steel to approx. 900oC, then keep it in a bath of sodium cyanide salt. Then wash off the salt with water or oil. The process causes little steel deformation and do not require further heat treatment for core material. However, the salt is poison to human. |
Where case hardening is used
- In order to have a material that is strong and hard enough for wear resistance, surface hardening (case hardening) method is used for such purposes.
- Components such as cam and cam roller are typical parts that required strong material to take the load, while hard on contact surface for wear resistance.